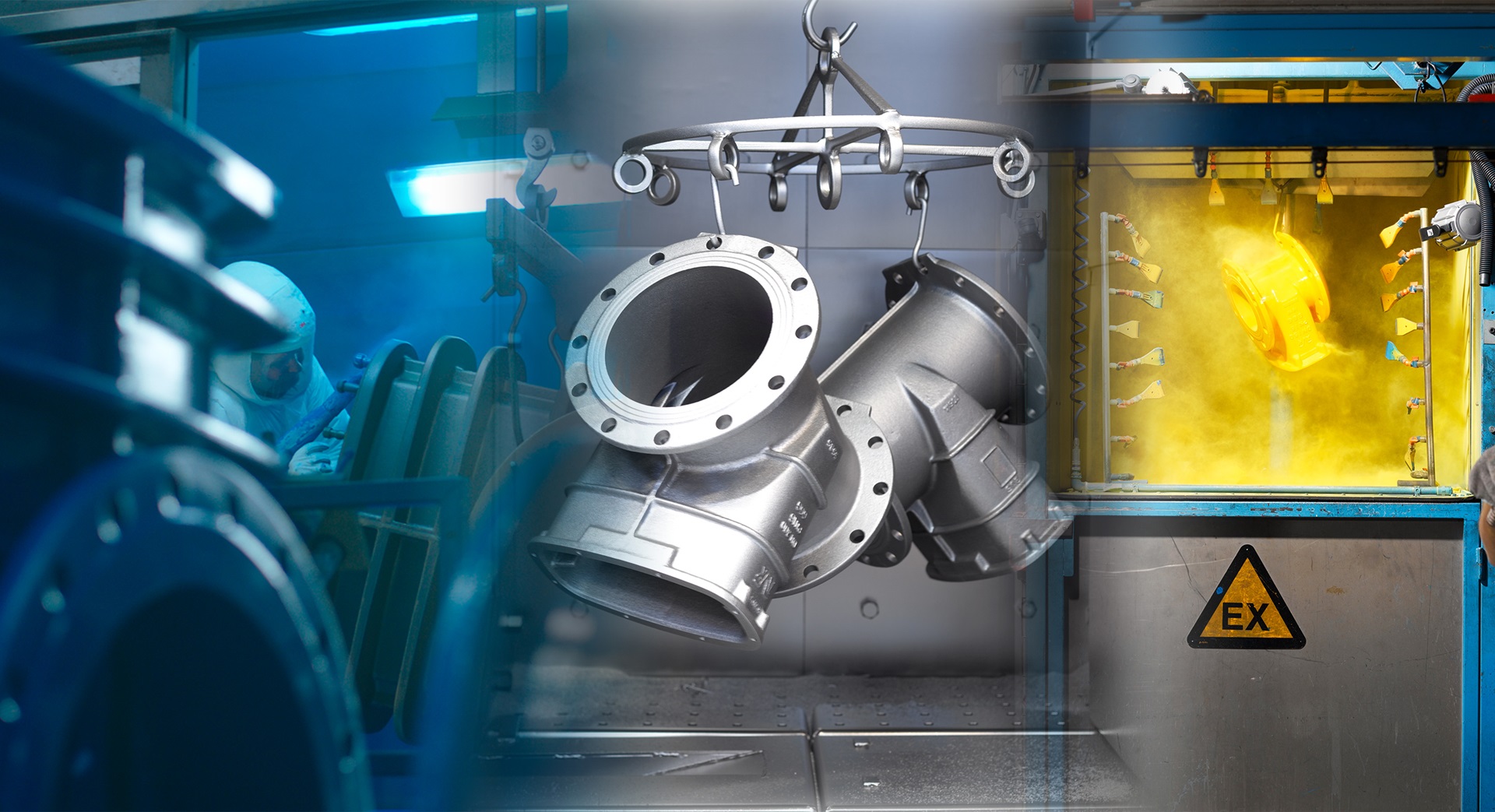
The high quality epoxy coating
At AVK, we offer the high-quality epoxy coatings that suits typical Vietnamese monsoon-influenced climate as of mainland Southeast Asia. We made it in-house where we are able to fully control of the supply chain. Before coating, we blast clean all cast parts according to ISO 12944-4 to make sure that any unevenness is cleaned to provide perfect adhesion of the coating for the high humidity and temperature of Vietnamese weather. And, this is how we proceed it:
Internal and external epoxy coating
The majority of AVK products are as standard with internal and external epoxy coating in compliance with DIN 3476 part 1, EN 14901 and GSK guidelines. The epoxy powder is applied on preheated components in a fluidised bed epoxy coating system. For selected products, such as small accessories or very big items, it is applied manually. The epoxy powder melts when in contact with the preheated components and cures when the components enter the cooling tunnel shortly after the coating process.
We control each batch of epoxy coated components to ensure a layer thickness of minimum 250 μ, a pore-free surface, high impact resistance and adequate curing as below test procedure:
- Coating thickness: The coating layer thickness shall be no less than 250 μm.
- Pore-free coating: The coating must be completely free of penetrating pores to avoid subsequent corrosion of the casting underneath. A 3V holiday detector with a brush electrode is used to electrically reveal and locate any pores in the coating.
- Impact resistance: The impact resistance test is carried out at room temperature right after the coating process by means of a stainless steel cylinder dropped on the coating surface through a one meter long tube corresponding to an impact energy of 5 Nm. After each impact the component is electrically tested, and no electrical breakthrough shall occur.
- Cross linkage: One drop of methyl isobutyl ketone are put on a horizontal epoxy resin coated surface of the test piece at room temperature. After 30 seconds the test area is wiped with a clean white cloth. It is checked that the test surface has not become neither matt nor smeared, and that the cloth remains clean. The test is carried out 24 hours after the coating process.
- Adhesion: The adhesion of the powder coating is tested on one side of a test plate four times a year for each coating plant according to GSK guidelines using the punch separation method according to DIN 24624. The coating thickness over a dispersed area of the test item shall be within the range 250 μm to 400 μm. The test pieces are immersed for seven days in deionised water at 90oC, and then dried in an oven for 3 hours. A conditioning phase of 3 to 5 days in normal atmosphere is then allowed to elapse. No blisters may arise during the period immersed in the water bath. The surface of the test piece is degreased and then roughened with abrasive paper. The roughened surface is cleaned from dust with oil-free compressed air and recleaned. The adhesion is tested with a minimum pulling force of >12 N/mm2.
- Cathodic disbonding: Cathodic disbonding tests are carried out on one of each type of component at least twice a year. No bubbles in the coating may develop during the test for cathodic disbonding. For this test, the coating thickness over a dispersed area of the test item shall be within the range 250 μm to 400μm.
In addition to our own tests, the independent GSK authorities control the adhesion and cathodic disbonding of the epoxy coating according to their guidelines.
The GSK Quality Assurance Association for Heavy-Duty Corrosion Protection of Valves and Fittings with Powder Coating (GSK e.V.) is the international industry network for businesses that coat valves and fittings with epoxy powder. GSK awards the RAL-GZ 662 Quality Mark (Gütezeichen) to companies who fulfil the strenuous quality-assurance requirements in accordance with the current Quality and Inspection Regulations. Click here for more information.
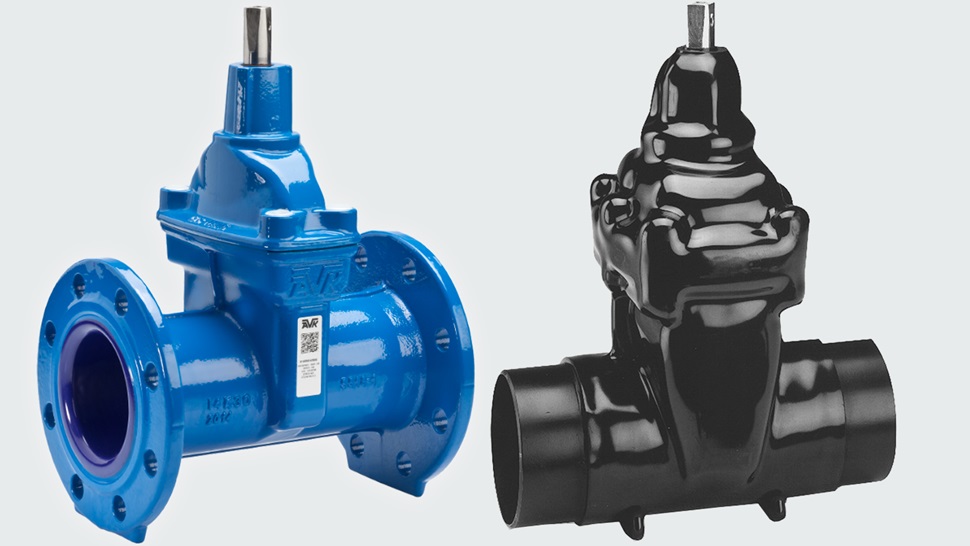